Rapid Prototyping Plastic: Revolutionizing the Manufacturing Industry
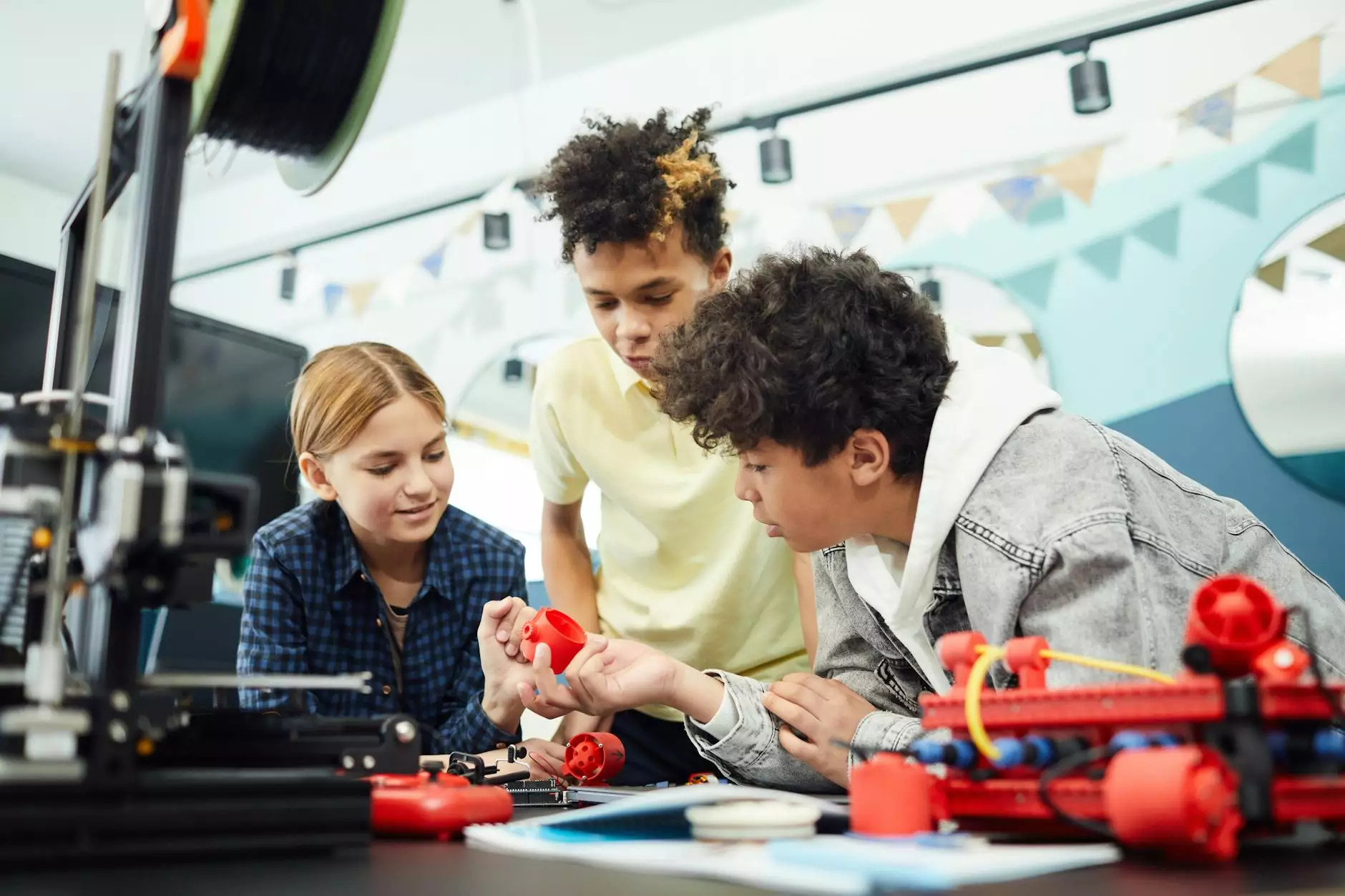
Rapid prototyping plastic is an innovative technology that has transformed the way businesses, particularly in the metal fabrication industry, approach product development. The ability to create prototypes quickly and efficiently allows manufacturers to streamline their processes, enhance creativity, and reduce costs. In this article, we will delve into the various aspects of rapid prototyping in plastic, its benefits, and how it stands as a critical asset in modern manufacturing.
What is Rapid Prototyping?
Rapid prototyping is a systematic approach to quickly fabricate a scale model of a physical part or assembly using 3D computer-aided design (CAD) data. It encompasses various techniques that enable the fast creation of models and parts. This technology allows businesses to test concepts and iterate designs more effectively than traditional manufacturing methods.
The Importance of Plastic in Rapid Prototyping
Plastic plays a pivotal role in rapid prototyping due to its versatility and ease of use. Several types of plastics can be employed, each with unique properties suitable for different applications:
- ABS (Acrylonitrile Butadiene Styrene): Known for its strength and durability, ABS is commonly used in prototype production.
- PLA (Polylactic Acid): This bio-based plastic is environmentally friendly and popular for basic prototyping.
- nylon: Known for its flexibility and toughness, nylon is ideal for functional prototypes.
- PVA (Polyvinyl Alcohol): Often used as a support material, PVA dissolves in water and is excellent for complex designs.
Benefits of Using Rapid Prototyping Plastic
The integration of rapid prototyping plastic into manufacturing workflows offers a myriad of benefits:
1. Reduced Time-to-Market
One of the most significant advantages of rapid prototyping is the drastic reduction in time-to-market. With the ability to create prototypes within days, businesses can collect feedback, make necessary adjustments, and launch products faster than ever before.
2. Cost-Effective Solutions
By leveraging rapid prototyping plastic, companies can save on the costs associated with traditional manufacturing. Prototyping in plastic requires less material and fewer resources, leading to substantial cost reductions in the early stages of product development.
3. Enhanced Design Flexibility
With rapid prototyping, designers have the freedom to explore various iterations of a concept without the significant financial implications associated with traditional tooling processes. This flexibility allows for greater innovation and creativity.
4. Improved Communication
Involving stakeholders in the design process is crucial for ensuring the final product meets market needs. Prototypes made from plastic offer a tangible representation of ideas, making it easier for teams to communicate concepts and gather valuable feedback.
5. Functional Testing
Rapid prototypes can be tested in real-world conditions, allowing businesses to assess performance before mass production begins. This testing phase can identify flaws and functionality issues early, saving future costs and time.
Applications of Rapid Prototyping Plastic in Metal Fabrication
The metal fabrication industry particularly benefits from rapid prototyping in plastic. Here are several applications where this technology shines:
1. Tooling and Manufacturing Aids
Prototypes created from rapid prototyping plastic can serve as tools to aid in the manufacturing processes, including jigs, fixtures, and templates, enhancing efficiency on the production floor.
2. Product Development
Initial product designs can be rapidly translated into physical prototypes using plastic. Metal fabricators can physically evaluate the forms, fit, and function of products, leading to better product outcomes.
3. Safety and Ergonomics Testing
Prototyping in plastic allows manufacturers to assess product ergonomics and safety features effectively. Changes can be made based on user feedback and testing results.
4. Marketing and Presentation Models
Creating visually appealing models for marketing campaigns can effectively communicate ideas to potential customers and stakeholders.
The Future of Rapid Prototyping Plastic
The future of rapid prototyping plastic is bright, with advancements in technology continuing to enhance capabilities. Innovations like 3D printing and new polymer developments will lead to:
- Improved material properties, leading to stronger and more durable prototypes.
- Greater accessibility for small businesses, allowing them to leverage advanced prototyping without massive investments.
- Integration of smart technologies, enabling more sophisticated and interactive prototypes.
Challenges and Considerations
While the benefits are substantial, it is essential to remain aware of the challenges associated with rapid prototyping with plastic materials:
1. Material Limitations
Each plastic comes with its limitations regarding strength, heat resistance, and finish quality. Understanding the specific requirements of each project is vital.
2. Post-Processing Requirements
Many plastic prototypes need post-processing to achieve the desired finish or strength. This additional step can lengthen the overall prototyping time.
3. Cost of Equipment
Advanced rapid prototyping technologies can require a significant financial investment, which may not be feasible for all businesses.
Conclusion
The integration of rapid prototyping plastic into business processes, especially in metal fabrication, represents a step toward a more agile and efficient manufacturing future. By embracing this technology, companies can enhance their product development processes, reduce costs, and improve time-to-market measures. As advancements continue, rapid prototyping is set to play an even more pivotal role in driving innovation across various industries.
Call to Action
If you’re ready to take your product development to the next level and explore how rapid prototyping plastic can benefit your business, visit Deep Mould today! Discover our tailored solutions in metal fabrication and gain a competitive edge in your market.