The Ultimate Guide to Bottle Label Applicators: Transforming Your Business Efficiency
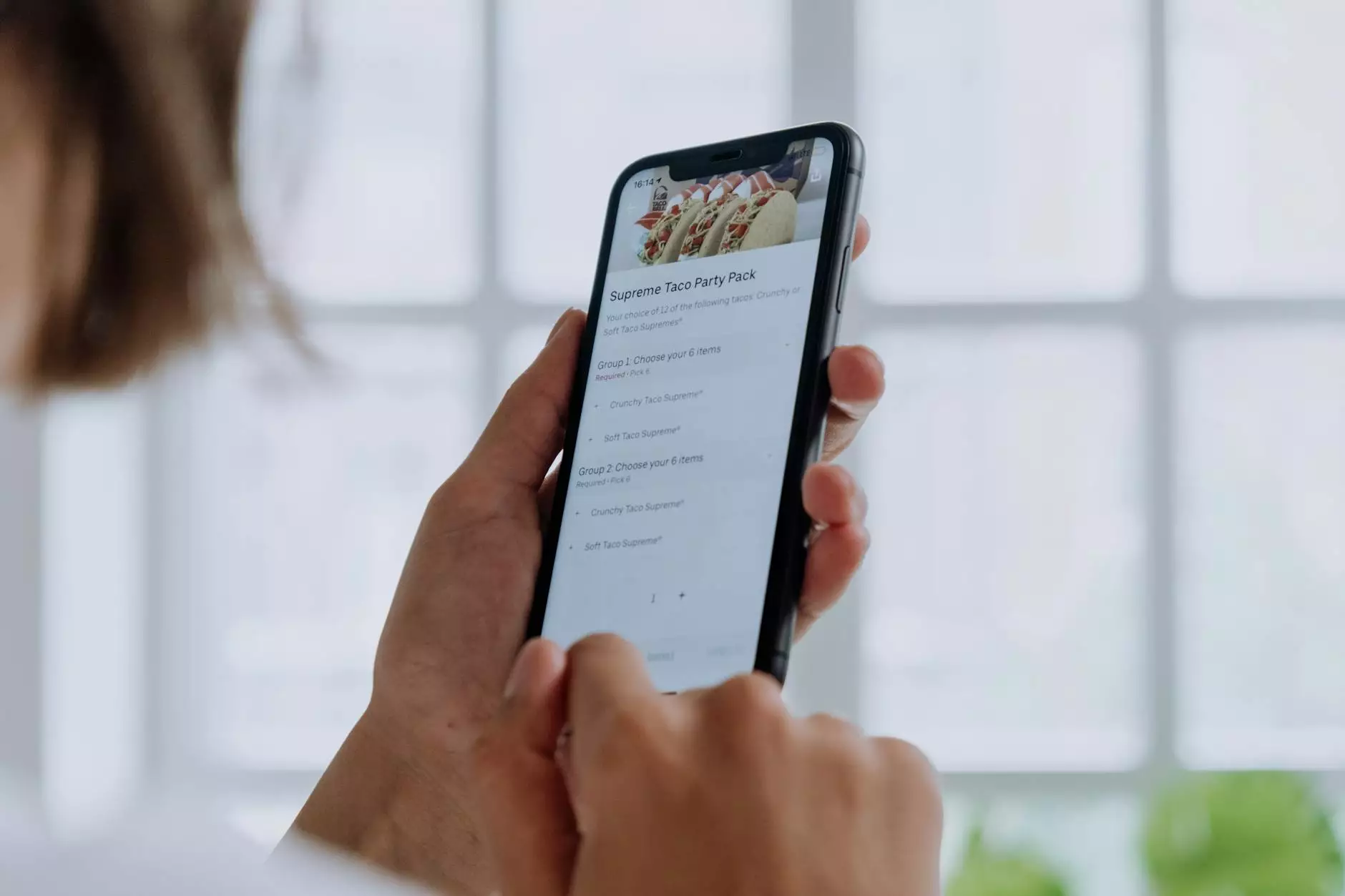
In today’s fast-paced business environment, efficiency is king. Companies across various industries are continually seeking ways to streamline their processes and improve the quality of their products. Among these innovations, the bottle label applicator stands out as an indispensable tool in the realm of printing services. This comprehensive guide delves deep into the world of bottle label applicators and how they can significantly enhance your business operations.
What is a Bottle Label Applicator?
A bottle label applicator is a sophisticated device designed to apply labels onto bottles with precision and speed. These machines are used in various sectors, including beverage production, cosmetics, pharmaceuticals, and food manufacturing. By automating the labeling process, businesses can reduce labor costs, minimize errors, and achieve a level of consistency that manual labeling simply cannot match.
How Bottle Label Applicators Work
While different models exist, most bottle label applicators share common technology and features. Understanding how these machines work can help businesses make informed decisions for their labeling needs.
Core Components of a Bottle Label Applicator
- Label Roll: Holds the labels, usually mounted on a spindle.
- Label Sensor: Detects the position of the label and ensures that it is applied at the correct moment.
- Applicator Arm: Mechanically applies the label to the bottle.
- Conveyor System: Moves bottles through the labeling machine smoothly.
- Control Panel: Allows for setting adjustments and monitoring the operation of the machine.
Benefits of Using a Bottle Label Applicator
Investing in a bottle label applicator offers numerous advantages, making it a worthwhile addition to your production line. Here are some key benefits:
1. Increased Efficiency
Automation of the labeling process ensures that labels are applied faster and more accurately than manual methods. This translates into a higher output and reduced operational costs.
2. Consistency and Quality
Using a bottle label applicator guarantees uniformity in label placement and application, leading to a more professional appearance of products. This consistency is crucial for brand reputation.
3. Reduced Labor Costs
With fewer workers needed to handle the labeling process, businesses can allocate manpower to other critical areas, thus optimizing overall labor costs.
4. Versatility
Modern bottle label applicators can handle a diverse range of bottle shapes and sizes, making them suitable for various industries. Whether it’s a round, square, or oval bottle, these applicators can be adjusted to fit different requirements.
5. Enhanced Production Speed
Label applicators can apply labels at incredible speeds, far surpassing human capabilities. This feature is particularly beneficial for companies that experience high demand and need to scale production accordingly.
Choosing the Right Bottle Label Applicator for Your Business
With a plethora of options available in the market, selecting the right bottle label applicator can be challenging. Here are some considerations to help guide your decision:
1. Product Specification
Understand the types of bottles your business uses. The applicator should be compatible with your product specifications, including size, shape, and label material.
2. Production Volume
Assess your production demands. If your business has high output requirements, consider a model that can handle larger volumes efficiently.
3. Ease of Use
Look for an applicator with an intuitive interface and easy setup to minimize training time for your employees.
4. Maintenance Requirements
Choose a machine that is easy to maintain, with accessible parts and clear maintenance instructions. This will help prevent downtime and increase productivity.
5. Budget
Finally, consider your budget. While it can be tempting to choose the cheapest option, consider the long-term investment and potential return on that investment with the right applicator.
Integrating a Bottle Label Applicator into Your Workflow
Once you have selected and purchased your bottle label applicator, it’s time to integrate it into your existing workflow. Here are some key steps to follow:
1. Staff Training
Proper training is vital for the successful use of your new technology. Ensure that your staff is well-versed in operating the machine safely and efficiently.
2. Workflow Adjustment
Consider adjusting your production line to incorporate the label applicator seamlessly. This might include changing the layout or modifying processes to enable smooth operations.
3. Regular Maintenance
Implement regular maintenance checks to keep the machine functioning at its best. This includes cleaning, checking for part wear, and ensuring that the label rolls are properly loaded.
4. Monitor Performance
Utilize performance metrics to measure the efficiency of your bottle label applicator. Pay attention to any issues that arise, and use this data to refine operations continually.
Case Studies: Success Stories with Bottle Label Applicators
Many businesses have transformed their operations through the successful use of a bottle label applicator. Here are a couple of inspiring examples:
Case Study 1: Beverage Industry
A mid-sized beverage company struggled with manual labeling, resulting in inconsistencies and delays. After investing in a high-speed bottle label applicator, they achieved:
- A 50% increase in labeling speed.
- A 30% reduction in labeling errors.
- A significant improvement in overall production efficiency.
Case Study 2: Cosmetics
A cosmetics manufacturer faced challenges with various bottle shapes and sizes. They implemented an adjustable bottle label applicator that allowed them:
- To label a wider variety of products with ease.
- To maintain a high-quality standard across their product line.
- To reduce labor by 40% in the labeling department.
Conclusion: The Future of Labeling with Bottle Label Applicators
As businesses continue to evolve in a competitive landscape, tools like the bottle label applicator will play a pivotal role in maintaining efficiency and quality. By automating the labeling process, companies not only improve their operational effectiveness but also uphold brand integrity through consistent product presentation.
The advantages of implementing a bottle label applicator extend beyond just speed and consistency; they represent a shift towards smarter manufacturing processes. In a world where every second and every detail count, investing in this technology aligns perfectly with future-ready business strategies.
For businesses exploring printing services, enhancing production with technologies like bottle label applicators ensures you not only meet but exceed customer expectations. Embrace the evolution of labeling—your business deserves it.