Mastering the Art of Die Casting Machining in Modern Metal Fabrication
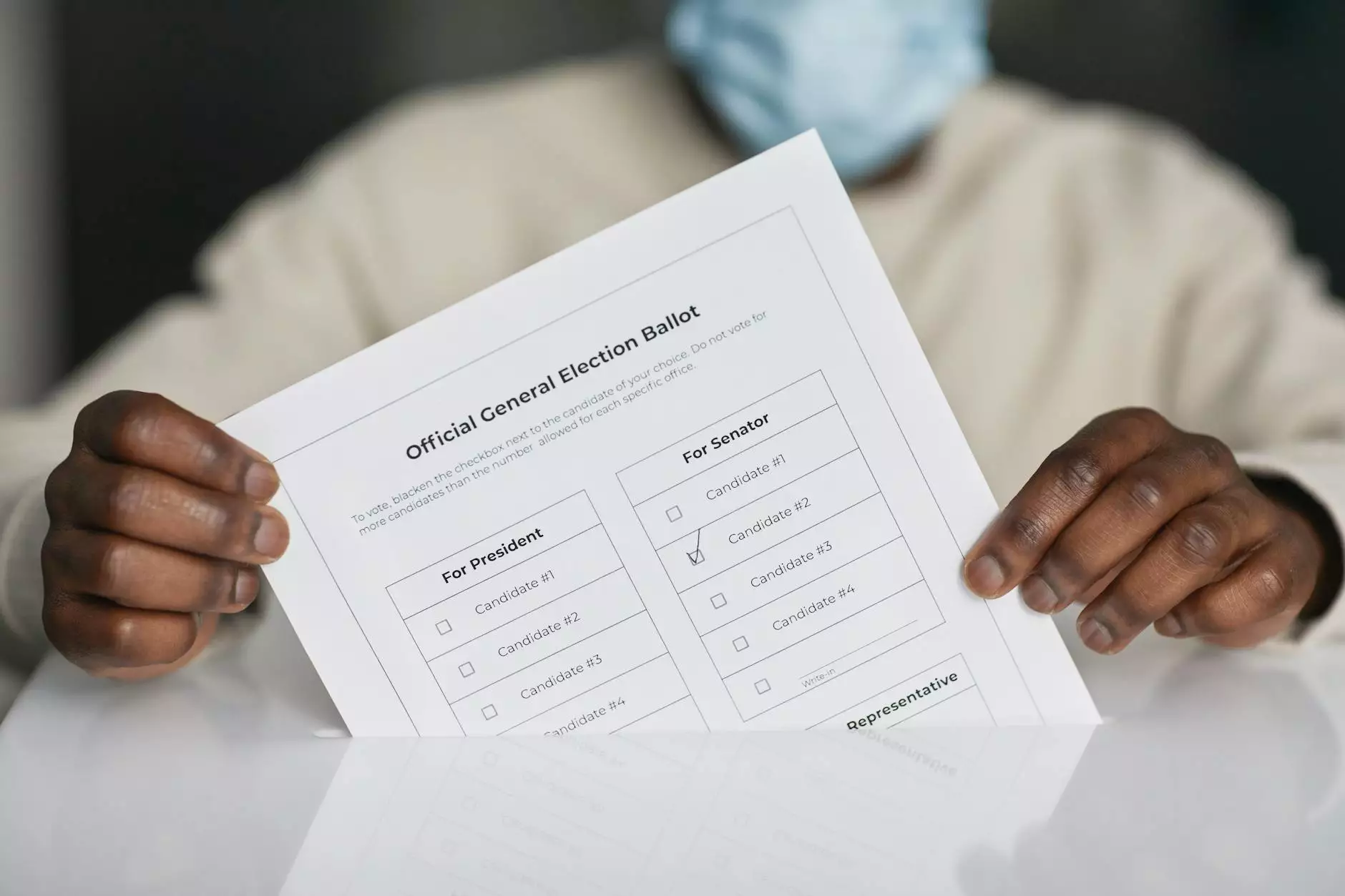
In the rapidly evolving domain of metal fabrication, die casting machining stands out as a cornerstone process that delivers unparalleled precision, efficiency, and high-volume production capabilities. As an industry-leading metal fabricator, DeepMould.net harnesses the power of die casting machining to produce complex, durable, and cost-effective metal components for a wide array of industries, including automotive, aerospace, consumer electronics, and industrial machinery.
Understanding Die Casting Machining: The Foundation of Quality Metal Components
Die casting machining is a manufacturing process that involves injecting molten metal into a precisely engineered metal mold (the die), allowing it to solidify into complex shapes with high dimensional accuracy. Once the initial casting is complete, machining operations refine the component to exact specifications, ensuring surface finish, tolerances, and intricate detail.
Why is Die Casting Machining Critical?
- High Precision: Ensures tight tolerances and intricate features that are impossible with traditional casting alone.
- Cost-Effective for Large Volumes: Allows rapid production of large batches with consistent quality.
- Complex Geometries: Supports complex designs, including internal channels, undercuts, and fine details.
- Superior Surface Finish: Achieves smoother surfaces, reducing or eliminating the need for extensive secondary finishing processes.
- Material Versatility: Compatible with numerous metals like aluminum, zinc, magnesium, and alloys.
Key Stages of Die Casting Machining in Metal Fabrication
1. Design and Prototype Development
Successful die casting machining starts with precise designs. Engineers utilize advanced CAD software to develop detailed models that account for manufacturing tolerances, thermal properties, and casting feasibility. Prototyping verifies design integrity before moving to production.
2. Die Fabrication
High-precision dies are crafted from hardened steel, designed to withstand extensive use while maintaining intricate details. CAD/CAM integration ensures that die dimensions adhere to exact specifications, facilitating consistent casting quality.
3. Die Casting Process
Molten metal is injected into the die under high pressure, filling cavities rapidly. The casting is then cooled and ejected, ready for machining. This stage requires meticulous control to optimize casting quality and minimize defects like porosity or misruns.
4. Machining and Finishing
Post-casting, components undergo precise die casting machining—a series of subtractive processes such as milling, drilling, turning, and grinding. These operations refine the part to meet exact dimensions, surface finishes, and functional requirements.
5. Quality Control and Testing
Rigorous inspection, including coordinate measurement machine (CMM) testing, X-ray inspection, and surface analysis, ensures the final product meets specified standards. Quality assurance is critical for applications requiring high reliability.
Advantages of Integrating Die Casting Machining Within Metal Fabrication Services
1. Exceptional Dimensional Accuracy and Tolerance Control
Incorporating die casting machining ensures that even the most complex components satisfy tight tolerances, typically within ±0.05 mm or better. This level of precision guarantees seamless assembly and optimal functionality of finished products.
2. Enhanced Surface Quality
While die castings inherently possess good surface finishes, machining further improves surface smoothness and detail sharpness, reducing the need for additional finishing steps and accelerating time-to-market.
3. Flexibility in Design Modifications
Even after initial die casting runs, minor adjustments to designs can be implemented during machining without modifying the entire die, fostering agility and innovation in product development.
4. Cost Savings in Large-Scale Production
By pairing die casting with machining, manufacturers reduce labor costs, minimize waste, and improve throughput—key factors in achieving competitive pricing for volume manufacturing.
Technical Innovations Elevating Die Casting Machining
The industry continuously adopts new technologies to enhance quality, productivity, and sustainability, including:
- Advanced CNC machining centers: Precision machines capable of complex multi-axis operations, reducing cycle times.
- Automation and Robotics: Automated loading, unloading, and inspection improve consistency and reduce human error.
- Simulation and Mold Flow Analysis: Pre-production simulations optimize casting and machining processes, preventing defects and reducing iterative trials.
- Sustainable Manufacturing: Use of environmentally friendly materials and energy-efficient machinery aligns with green manufacturing goals.
Why Choose DeepMould.net for Die Casting Machining?
DeepMould.net has established itself as a leader in metal fabrication services, especially when it comes to die casting machining. Our commitment to excellence is reflected in:
- Cutting-Edge Technology: We leverage the latest CNC machines, robotic automation, and die casting innovations to ensure superior quality.
- Experienced Engineering Team: Our engineers collaborate with clients from concept through production, providing tailored solutions for complex projects.
- Sustainable Practices: We prioritize eco-friendly processes, waste reduction, and energy efficiency.
- Rigorous Quality Control: Every component undergoes comprehensive inspections to meet international standards.
- Customer-Centric Approach: We emphasize transparent communication, timely delivery, and flexible production runs to meet your exact needs.
Industry Applications of Die Casting Machining
The versatility of die casting machining makes it indispensable across diverse industries, including:
Automotive Industry
Manufacturing engine blocks, transmission cases, and intricate structural components that demand precision and durability.
Aerospace
Producing lightweight yet robust parts such as housings, brackets, and connectors that adhere to stringent safety standards.
Electronics and Home Appliances
Creating housings, frames, and casing designs with fine details and high surface quality for consumer products.
Industrial Machinery
Supplying durable components like gearboxes, valve bodies, and structural supports with complex geometries.
The Future of Die Casting Machining in Metal Fabrication
As manufacturing technology advances, the role of die casting machining is set to expand further. Emerging trends include:
- Smart Manufacturing: Integration of Industry 4.0 principles for real-time monitoring and predictive maintenance.
- Material Innovation: Development of new alloys with superior strength-to-weight ratios and corrosion resistance.
- Energy-Efficient Processes: Adoption of sustainable, low-energy casting and machining methods.
- Customization and Short Runs: Greater flexibility to produce tailor-made components with rapid turnaround times.
Conclusion: Unlocking Business Potential Through Expert Die Casting Machining
In conclusion, the strategic integration of die casting machining within a comprehensive metal fabrication framework offers unparalleled advantages in producing high-quality, complex, and cost-effective components. Leading industry players like DeepMould.net exemplify the benefits of adopting advanced technology, skilled engineering, and sustainable practices to excel in competitive markets.
For companies seeking to elevate their manufacturing capabilities, investing in expert die casting machining services is not just an upgrade—it's a decisive step toward innovation, efficiency, and excellence in metal fabrication.