Transforming Business Success with Design for Additive Manufacturing
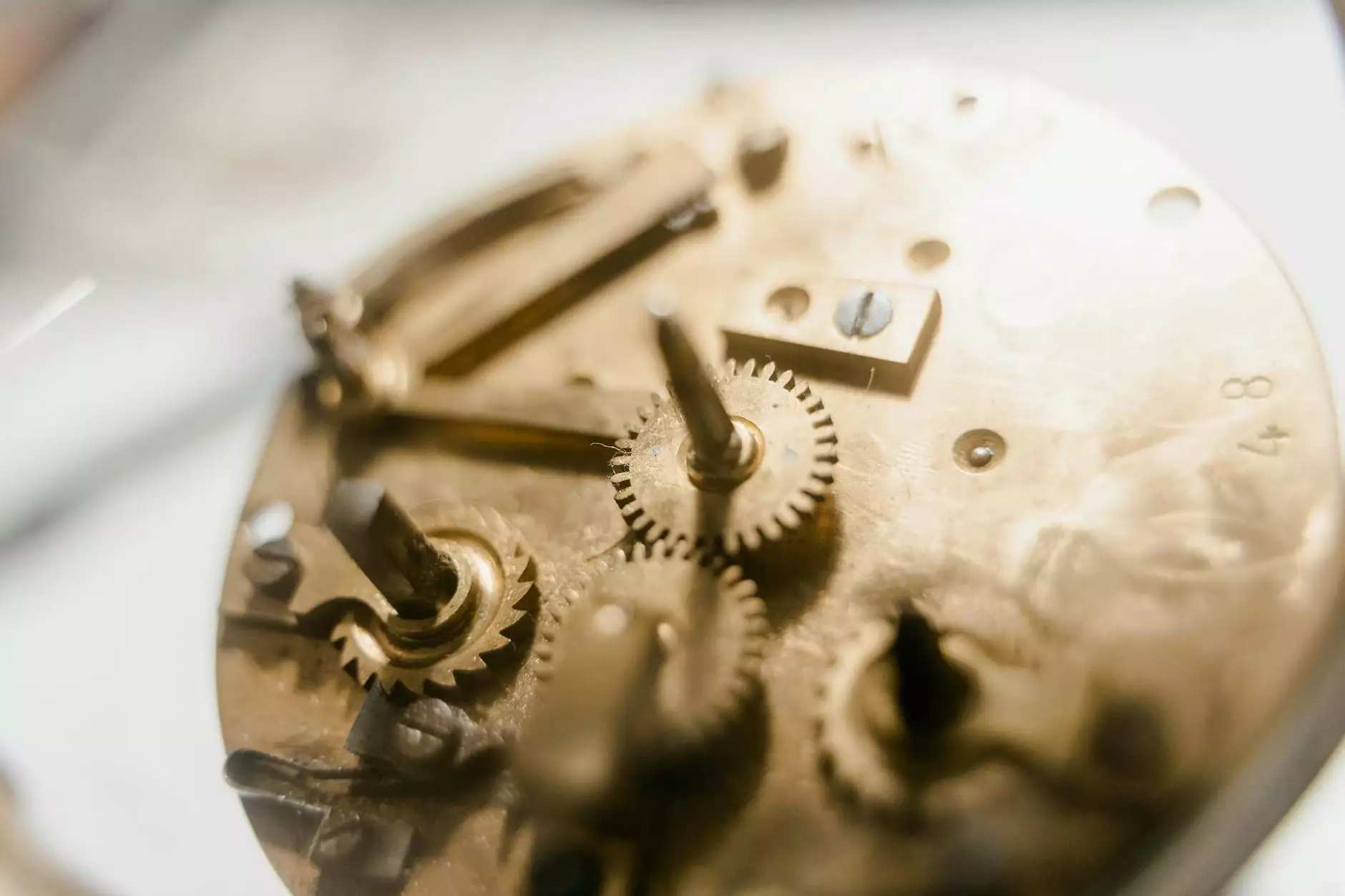
In the rapidly evolving landscape of modern manufacturing, design for additive manufacturing (DfAM) has emerged as a game-changing approach that empowers businesses to innovate, streamline production, and achieve unprecedented levels of customization and efficiency. As companies like arti90.com continue to spearhead advancements in art supplies, product design, and 3D printing, understanding and leveraging DfAM principles becomes essential for maintaining competitive edge in today's dynamic market environment.
What Is Design for Additive Manufacturing? An In-Depth Overview
Design for additive manufacturing, often abbreviated as DfAM, refers to the specialized process of designing products and components with the specific capabilities and constraints of additive manufacturing (AM) technologies in mind. Unlike traditional manufacturing, which often requires multiple steps, molds, or extensive tooling, AM builds objects layer-by-layer directly from digital models. This unique process unlocks new design possibilities that were previously unattainable through conventional methods.
At its core, design for additive manufacturing emphasizes flexibility, innovation, and optimization. It encourages designers to rethink traditional design paradigms, exploiting features such as complex geometries, internal structures, and lightweighting that are exclusive to AM techniques like 3D printing. Integrating DfAM principles from the outset ensures that products are not only manufacturable but also optimized for performance, cost, and sustainability.
The Strategic Business Advantages of Incorporating Design for Additive Manufacturing
Embracing design for additive manufacturing delivers a multitude of tangible benefits that significantly impact a company's growth trajectory:
- Rapid Prototyping and Iteration: Accelerate the product development cycle by quickly turning digital concepts into physical prototypes, enabling faster testing, validation, and refinement.
- Complex Geometries and Customization: Create intricate, lightweight, and highly personalized products that were impossible with traditional manufacturing methods.
- Cost Reduction: Minimize the need for costly tooling, molds, or assembly lines, especially for low to medium production volumes.
- Supply Chain Flexibility: Enable decentralized manufacturing, just-in-time production, and on-demand customization, reducing inventory costs and lead times.
- Sustainable Production: Reduce waste and material consumption by optimizing designs and utilizing eco-friendly materials.
For businesses in sectors like art supplies, product design, and 3D printing, these advantages translate into increased innovation capacity, expansion into niche markets, and enhanced customer engagement through bespoke offerings.
Key Considerations in Design for Additive Manufacturing Strategy
To harness the full potential of design for additive manufacturing, companies must adopt a comprehensive strategy that encompasses several critical aspects:
Material Selection and Compatibility
The choice of material directly influences the manufacturability, durability, and finish quality of AM products. Advances in printable materials, such as high-performance polymers, metals, and composites, allow tailored solutions aligned with business requirements.
Geometry Optimization
Design geometries that leverage AM's strengths—such as organic shapes, internal channels, and lattice structures—to reduce weight, enhance strength, or embed functional features.
Design Simplicity versus Complexity
While AM enables complex designs, it is vital to balance intricacy with manufacturing constraints like printer build volume, support structure removal, and print resolution.
Cost and Production Scalability
Evaluate the cost implications of design modifications and determine the optimal production volume that justifies the initial design effort versus traditional manufacturing methods.
Integration with Digital Manufacturing Ecosystems
Seamlessly integrating digital workflows, from CAD modeling to slicing and post-processing, ensures streamlined production and quality control.
Implementing Design for Additive Manufacturing in Business Operations
Successfully integrating design for additive manufacturing into your business involves multiple steps:
- Education and Training: Equip your design and engineering teams with knowledge about AM technologies and DfAM principles.
- Collaborate with AM Experts: Partner with specialized providers or consult experts to optimize your product designs.
- Revise Design Processes: Incorporate DfAM guidelines early in the product development cycle to maximize benefits.
- Invest in Quality Equipment: Choose appropriate 3D printers and material options aligned with your business goals.
- Continuous Innovation: Regularly review and refine design strategies based on technological advancements and market feedback.
Adoption of these steps can lead to a competitive advantage, offering unique products, faster time-to-market, and reduced operational costs.
The Role of Art Supplies, Product Design, and 3D Printing in Design for Additive Manufacturing
Specifically, in the domains of art supplies, product design, and 3D printing, design for additive manufacturing opens up innovative pathways:
- Art Supplies: Creating customized, collectible, or functional art pieces with intricate details and personalized features that appeal to niche markets.
- Product Design: Designing consumer products with integrated functionalities, reducing parts count, and facilitating aesthetic flexibility.
- 3D Printing: Facilitating on-demand production, rapid iteration, and complex internal structures for high-performance applications.
These sectors stand to benefit immensely from the flexibility, speed, and creative potential that design for additive manufacturing offers.
Future Trends and Innovations in Design for Additive Manufacturing
The future of design for additive manufacturing is poised for rapid growth as technological innovations continue to emerge:
- AI-Driven Design Optimization: Artificial intelligence algorithms will enable autonomous design iteration, optimizing for weight, strength, and material usage.
- Multi-Material Printing: Advanced printers will facilitate multi-material parts with tailored properties, expanding design possibilities.
- Sustainable Manufacturing: Material recycling and eco-friendly resins will make AM even more sustainable.
- Increased Accessibility: Lower costs and user-friendly software will democratize access to AM and DfAM practices for small and medium-sized enterprises.
Staying ahead in this evolving landscape requires continuous learning, innovation, and strategic implementation of design for additive manufacturing.
Conclusion: Unlocking Business Potential through Cutting-Edge Design Strategies
In conclusion, design for additive manufacturing stands as a pivotal strategy that empowers businesses to innovate rapidly, reduce costs, and create highly customizable, high-quality products. Whether operating within art supplies, product design, or 3D printing sectors, embracing DfAM principles can revolutionize operations and open new revenue streams.
For companies like arti90.com, positioning at the forefront of design for additive manufacturing adoption means fostering a culture of continuous innovation, building expertise in emerging technologies, and aligning design processes withadvanced AM capabilities. By doing so, your business will not only adapt to the future but also shape it.
Elevate your business today by investing in design for additive manufacturing-driven strategies, and unlock limitless possibilities for growth, creativity, and competitive superiority.